In the world of construction, a mechanical rough-in checklist is an essential tool for ensuring that all necessary mechanical systems are properly installed and functioning before the final stages of a building project. but what is a mechanical rough in checklist? It serves as a comprehensive guide for construction professionals to verify that everything is in order and meets the required standards. From plumbing to electrical systems, this checklist covers all aspects of the mechanical rough-in process.
Note: you might also see the terms ‘rough in mechanical checklist’ and ‘rough mechanical checklist’ – they amount to the same thing.
Understanding the Basics of Mechanical Rough-Ins
What are they?
Before we dive into the importance of a mechanical rough-in checklist, let’s first understand what a mechanical rough-in entails. In the building trade, a mechanical rough-in refers to the installation of essential mechanical systems, such as HVAC (heating, ventilation, and air conditioning), plumbing, and electrical systems. These systems are crucial for the overall functionality and comfort of the building. The mechanical rough-in stage involves the installation of the necessary infrastructure, including pipes, wires, conduits, and other components, before the walls and ceilings are completed.
During the mechanical rough-in process, skilled technicians meticulously plan and execute the installation of these vital systems. For instance, in the case of HVAC systems, ductwork is carefully laid out to ensure optimal airflow and temperature control throughout the building. Plumbing rough-ins involve the precise positioning of pipes, valves, and fixtures to guarantee efficient water supply and drainage. Electricians meticulously run wires, install outlets, switches, and circuit breakers, ensuring a safe and reliable electrical system.
It is important to note that the mechanical rough-in stage is a critical phase in the construction process. This is because any mistakes or oversights during this stage can lead to costly and time-consuming issues later on. For example, improper placement of HVAC ducts can result in uneven heating or cooling, leading to discomfort for occupants and potential energy inefficiencies. Similarly, mistakes in plumbing rough-ins can result in leaks, water damage, or poor water pressure, affecting the functionality and longevity of the building. Electrical errors can pose safety hazards, such as electrical shocks or fire risks.
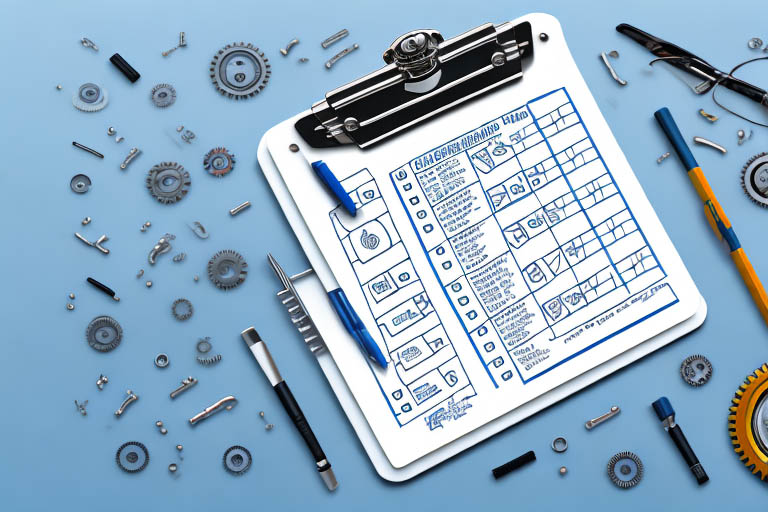
Mechanical Checklist
Proper Installation
A comprehensive mechanical rough-in checklist is essential to ensure that all necessary steps are taken and all components are properly installed. This checklist serves as a guide for technicians, ensuring that they cover all the crucial aspects of the rough-in process. It includes items such as verifying the correct placement of pipes, wires, and ducts, checking for proper insulation and sealing, and confirming that all connections are secure and up to code.
Minimise Errors
By following a mechanical rough-in checklist, construction professionals can minimize the risk of errors and ensure that the mechanical systems are installed correctly. This not only guarantees the functionality and comfort of the building but also saves time and money by avoiding costly rework or repairs. So, next time you see a building under construction, remember the intricate work that goes into the mechanical rough-in stage, laying the foundation for a well-functioning and efficient space.
The Importance of a Mechanical Rough-In Checklist
Avoid Rework
Having a mechanical rough-in checklist is vital for several reasons. Firstly, it ensures that all necessary components are properly installed according to the building plans and specifications. This step helps avoid costly rework and delays during the final stages of construction. Secondly, it serves as a quality control measure, guaranteeing that the mechanical systems are safe, efficient, and compliant with building codes and regulations. Lastly, the checklist acts as a documentation tool, providing a clear record of the work completed and serving as a reference for future maintenance and inspections.
When it comes to construction projects, attention to detail is crucial. A mechanical rough-in checklist plays a significant role in ensuring that every aspect of the mechanical systems is thoroughly assessed and accounted for. By meticulously following the checklist, contractors can be confident that nothing is overlooked or left to chance.
One of the key advantages of using a mechanical rough-in checklist is the prevention of costly rework. Imagine the frustration and financial burden that can arise if a component is missed during installation and is only discovered during the final stages of construction. Not only does this lead to delays, but it also requires additional labour and materials to rectify the issue. By diligently following the checklist, contractors can avoid such setbacks and keep the project on track.
Quality Control
Moreover, the checklist serves as a quality control measure, ensuring that the mechanical systems meet the necessary safety standards and regulations. This is of utmost importance, as faulty installations can pose serious risks to the occupants of the building. By adhering to the checklist, contractors can verify that all connections are secure, all equipment is properly calibrated, and all safety measures are in place. This not only protects the well-being of those who will use the building but also safeguards the reputation of the construction company.
Provides Documentation
Additionally, the checklist acts as a valuable documentation tool. It provides a comprehensive record of the work completed during the mechanical rough-in phase, including details of the components installed, their specifications, and any adjustments made. This documentation can prove invaluable for future maintenance and inspections. When conducting routine maintenance or inspections, having access to a detailed checklist can help technicians identify any potential issues or areas that require attention. It also ensures that any modifications or upgrades can be carried out efficiently, as the checklist provides a clear understanding of the existing system.
In conclusion, a mechanical rough-in checklist is an indispensable tool for any construction project. Its role in preventing costly rework, ensuring quality control, and providing valuable documentation cannot be overstated. By diligently following the checklist, contractors can ensure that the mechanical systems are installed correctly, meeting all safety standards and regulations. So, next time you embark on a construction project, make sure to have a comprehensive mechanical rough-in checklist in place.
Key Components of a Mechanical Rough-In Checklist
A well-designed mechanical rough-in checklist covers various components relevant to the specific project. This includes but is not limited to:
- Plumbing Systems: Check for proper installation of pipes, drains, fixtures, and valves. Ensure all connections are secure and leak-free.
- Electrical Systems: Verify that wiring, circuits, switches, and outlets are correctly installed and properly labeled.
- HVAC Systems: Inspect the installation of ductwork, vents, fans, and condensing units. Test the functionality of heating and cooling systems.
These are just a few examples of what can be included in a mechanical rough-in checklist. Depending on the complexity and scope of the project, additional items may need to be added to ensure thoroughness and accuracy.
Fire Protection Systems
Another crucial component to consider in a mechanical rough-in checklist is fire protection systems. Ensuring the proper installation of fire sprinklers, smoke detectors, and fire alarms is essential for the safety of the building and its occupants. The checklist should include a thorough inspection of these systems, checking for correct placement, functionality, and compliance with fire safety regulations.
In addition to fire protection systems, it is important to include a section on ventilation systems in the checklist. This involves examining the installation of exhaust fans, air vents, and air circulation systems. Proper ventilation is vital for maintaining indoor air quality and preventing the build-up of harmful pollutants or excessive moisture, which can lead to health issues and structural damage.
Other Uses
Moreover, a comprehensive mechanical rough-in checklist should address the installation of specialized systems that may be required for specific projects. For example, in a commercial kitchen, the checklist should cover the installation of commercial-grade kitchen equipment, such as exhaust hoods, grease traps, and fire suppression systems. In a laboratory setting, the checklist should include the installation of fume hoods, gas lines, and emergency shut-off valves.
By expanding the checklist to include these additional components, you can ensure that all relevant aspects of the mechanical rough-in are thoroughly inspected and accounted for. This level of detail and attention will contribute to the overall success and quality of the project.
Step-by-Step Guide to Conducting a Mechanical Rough-In Checklist
Are you ready to dive into the world of mechanical rough-in checklists? Let’s get started! This step-by-step guide will walk you through the inspection process, ensuring that no detail goes unnoticed. So, grab your building plans, put on your inspector hat, and let’s begin!
Requirements & Standards
Start by reviewing the building plans and specifications to familiarize yourself with the requirements and standards. This crucial step sets the foundation for a successful inspection. Take the time to understand the intricacies of the project, ensuring that you’re well-equipped to assess the mechanical systems.
Plumbing
Now, let’s dive into the plumbing systems. This is where you’ll inspect the intricate network of pipes and connections that keep water flowing smoothly throughout the building. Check for proper installation, connections, and adherence to plumbing codes. Look out for any signs of leaks or potential issues that may arise in the future. Remember, attention to detail is key!
Electrical Systems
Moving on to the electrical systems, it’s time to put your detective hat on. Verify the correct placement and connection of wiring, circuits, and outlets. Test the functionality of switches and lighting fixtures, ensuring that everything is in perfect working order. Safety is paramount here, so keep an eye out for any potential hazards or code violations.
HVAC
HVAC systems are the heart and soul of any building, responsible for keeping occupants comfortable year-round. Inspect the installation of ductwork, vents, and equipment. Ensure proper airflow and functionality of heating and cooling units. Take a moment to appreciate the intricate design and engineering that goes into these systems, marvelling at the seamless integration of technology and comfort.
Details
As you continue through the checklist, addressing each component and system outlined, pay close attention to the details. Take note of any issues or deficiencies that need to be addressed before moving forward. Remember, your meticulousness will ensure a smooth transition from rough-in to the final stages of construction.
Review the findings
This time is your opportunity to reflect on the inspection, evaluating the overall quality of the mechanical systems. Make any necessary corrections or improvements, ensuring that everything is up to par. Your attention to detail will ensure a safe and efficient building for years to come.
Documentation
Finally, document the completion of the mechanical rough-in checklist for future reference and inspections. This record will serve as a valuable resource, providing a comprehensive overview of the mechanical systems’ installation. It will also aid in future maintenance and troubleshooting, allowing for swift resolution of any issues that may arise.
And there you have it! A step-by-step guide to conducting a mechanical rough-in checklist. By following these instructions and paying close attention to detail, you’ll ensure that the mechanical systems in your building are top-notch. So, go forth and inspect things with confidence!
Common Mistakes to Avoid in Mechanical Rough-Ins
Despite the importance of a mechanical rough-in checklist, mistakes can still occur. Being aware of common pitfalls can help avoid unnecessary setbacks and issues. Some common mistakes to avoid during mechanical rough-ins include:
- Poorly aligned pipes or ductwork, resulting in restricted airflow or leaks.
- Inadequate insulation of pipes, leading to potential heat loss or condensation issues.
- Inaccurate wiring and poor labelling, causing confusion and potential safety hazards.
- Failure to comply with building codes and regulations, resulting in potential fines or rework.
Tools and Equipment Required for a Successful Mechanical Rough-In
To carry out a mechanical rough-in checklist effectively, certain tools and equipment are necessary. These include:
- Measuring tools, such as tape measures or laser levels, for accurate placement of components.
- Plumbing tools, including wrenches, pipe cutters, and thread sealants.
- Electrical tools, such as wire strippers, electrical testers, and conduit benders.
- HVAC tools, including duct cutters, crimping tools, and refrigerant gauges.
- Safety equipment, such as gloves, goggles, and protective clothing.
Tips for Efficiently Completing a Mechanical Rough-In Checklist
Completing a mechanical rough-in checklist requires careful attention to detail and efficient work methods. Here are some tips to help you streamline the process:
- Stay organized: Have a well-structured checklist and a clear understanding of the project requirements.
- Communicate effectively: Coordinate with other tradespeople involved in the project to ensure smooth progress.
- Work systematically: Follow a logical sequence when conducting inspections and address any issues promptly.
- Use technology: Consider utilizing digital tools, such as mobile apps to enhance efficiency and accuracy.
- Seek professional guidance: If in doubt, consult with experienced professionals or building inspectors for guidance.
Best Practices for Inspecting a Mechanical Rough-In
Inspecting a mechanical rough-in involves both technical know-how and a keen eye for detail. Here are some best practices to keep in mind:
- Follow industry standards: Familiarize yourself with local and national building codes to ensure compliance.
- Perform thorough inspections: Leave no stone unturned when verifying the installation and functionality of mechanical systems.
- Document findings: Take detailed notes and photographs as evidence of compliance or areas requiring improvement.
- Be proactive: Address any issues or deviations from the plans immediately to minimize rework and delays.
- Double-check measurements: Precision is crucial in ensuring proper alignment and fit of components.
How to Ensure Compliance with Building Codes in Mechanical Rough-Ins
Building codes and regulations exist to ensure the safety, functionality, and durability of buildings. When conducting a mechanical rough-in, it is essential to adhere to these codes. Here’s how you can ensure compliance:
- Stay informed: Regularly update your knowledge of current building codes and any specific requirements for your work area.
- Seek guidance: Consult with building inspectors or code enforcement officers if you are unsure about any code interpretations or requirements.
- Collaborate with other trades: Communicate and coordinate with other trades involved in the project to ensure compliance with overlapping requirements.
Benefits of Using a Digital Checklist for Mechanical Rough-Ins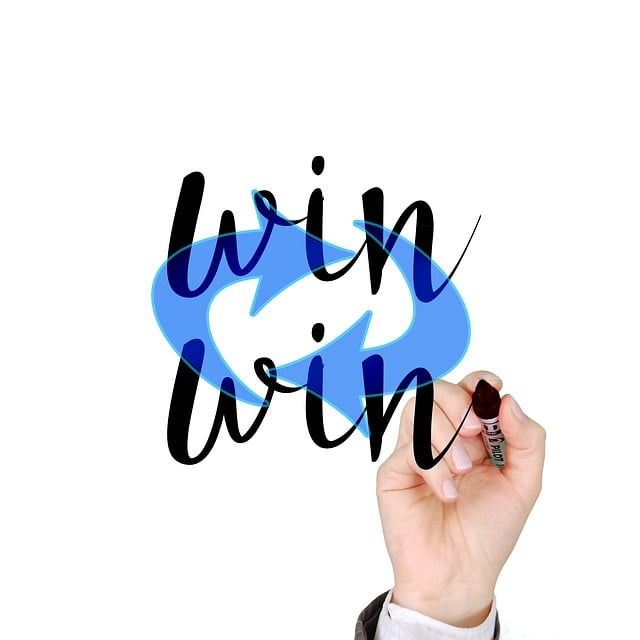
In today’s digital age, the use of technology has become increasingly prevalent in the construction industry. With mechanical rough-ins, utilizing a digital checklist can bring several benefits, including:
- Enhanced efficiency: Digital checklists allow for faster data entry, automated calculations, and real-time collaboration.
- Improved accuracy: Digital tools can help minimize human errors, ensuring all required inspections and tests are completed.
- Centralized documentation: Digital checklists provide a centralized platform to store, organize, and retrieve project documentation conveniently.
- Cost savings: Going paperless by using digital checklists can reduce printing and storage costs, as well as saving time spent on manual documentation.
By embracing technology and leveraging the advantages of digital checklists, construction professionals can streamline the mechanical rough-in process and deliver projects more efficiently.
Why not build you specific rough-in mechanical checklist in Brightchecker!
Additional Reading
More Helpful Content
Visit our Homepage